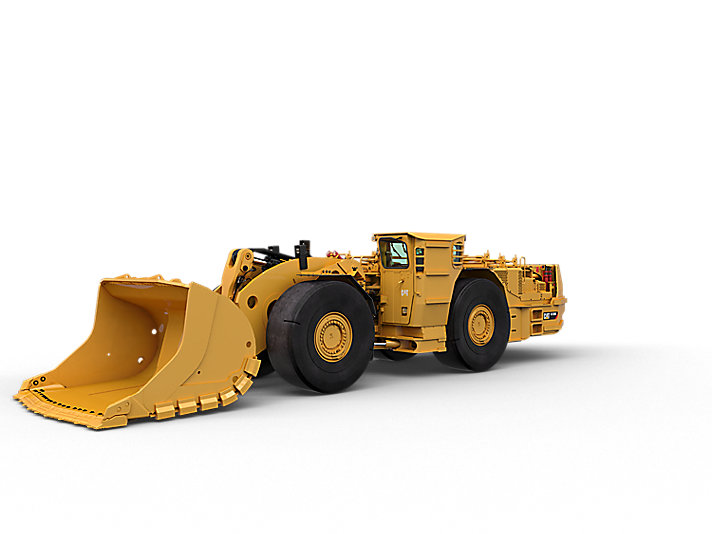
Cat Underground hard rock R1700
Product Feature
Structures
Strength through Advanced Technology and Validation
We’ve integrated more tie down and lift points to this machine to help drop it down a mine shaft. The new optional tow hook is bolted on for quick removal and installation.
Technology Enabled Strength
The R1700 is a stronger, more robust machine which is clearly reflected in the new design of its structures. Using the latest engineering design and validation tools, we’ve given this frame strength where it needs it most, and saved weight in other locations.
The Non Engine End Frame
The front frame section has a new four plate design with a new, fully integrated front axle support casting at its base. This new casting absorbs greater impact, vibration and tram loads that come with the growth of the machine capacity and weight.
Lift Arms and Bucket Linkage
The lift arms on the R1700 are visibly stronger with additional steel thicknesses in key areas.
This new design allowed us to widen access to service points to the front frame and hydraulic components.
Our bucket linkage, cylinder attachment points and cylinder sizes have been updated to greatly improve the mechanics of loading.
Complimenting this new geometry are brand new, redesigned buckets for this machine.
The Engine End Frame
The engine end frame was a complete redesign. With the addition of (optional) Stage V aftertreatment, the frame grew slightly. The redesign allowed us to improve:
The center of gravity.
The machine’s loading characteristics.
Ride quality for the operator.
You’ll notice that we’ve angled the rear of the frame while maintaining our departure angle to minimize impact damage, and we’ve increased wear material coverage.
Two castings have been incorporated into the rear of the frame as counterweights and to help manage loads through the frame.
Service access points underneath the machine have been made larger.
Where previous generations of this machine had two frame-integrated fuel tanks, the R1700 has a single bolted in fuel tank that is simple to maintain and offers approximately 12 hours of operation before refueling.
The Hitch
Like the newly expanded service access on the front linkage, we have redesigned the hitch with:
More space for service technicians to work.
New and larger pins connecting the two frames.
Clean and simplified hydraulic routings across the hitch.
Power Train – Production Is the Priority
The Cat C13 ACERT Diesel Engine
All new levels of power and performance for the R1700 start with the engine. Where the R1700G made good use of the power from the C11, this new machine and its performance goals demanded more – so we moved up in size to the C13 ACERT.
The C13 ACERT is a heavy-duty performer with an in-line, 6-cylinder configuration that is turbo-charged and air-to-air aftercooled. In the R1700, this engine is set at a horsepower rating of:
257 kW or 345 hp at 1,100 rpm for Stage V engines.
269 kW or 361 hp for engines that emit equivalent to Tier 3/Stage IIIA or Tier 2/Stage II VR (ventilation reduction).
The C13 ACERT is capable of high altitude operation and will begin to derate after:
Altitude 2895 m (9,500 ft) for Stage V engines.
Altitude 3505 m (11,500 ft) for Tier 3/Stage IIIA engines.
Altitude 3200 m (10,500 ft) for Tier 2/Stage II VR engines.
The C13 ACERT features the Cat MEUI (mechanically-actuated electronic unit injection) system for providing high pressure injection across the engines operating speed range. ACERT requires multiple injections of highly pressurized and atomized fuel during the combustion cycle. Precisely shaping the combustion cycle lowers combustion chamber temperatures, which generates fewer emissions, optimizes fuel combustion; translating into more work per liter (gallon) of fuel burned.
Aftertreatment for the Stage V engine configuration is chassis mounted for convenience and includes a Diesel Emission Fluid (DEF) tank sized to match the 12-hour capacity of the fuel tank. Aftertreatment components are carefully guarded and heat wrapped. The system uses regeneration to manage emissions inside the Clean Emissions Module (CEM). Regeneration can be set to automatic – the operator is informed when regeneration is happening, and the machine takes care of the process while continuing to operate.
Lock-Up Clutch Torque Converter
Part of the speed on grade improvement comes from a new lock-up clutch torque converter. It is the same component used in our larger LHD range and it has been sized for extreme durability. It engages automatically as the machine shifts into second gear.
Transmission
The Cat transmission on this machine is also newly resized for durability. It is now governed by our APECS software that allows the transmission to comfortably shift under higher torque conditions. This allows the machine to climb grades more quickly by reducing lost momentum between shifts, and it can potentially allow the machine to climb in a lower gear saving fuel. This will be determined by your mine conditions.
ECPC or Electronic Clutch Pressure Control is working in tandem with APECS to reduce pressure spikes inside the transmission and ensure its long-term durability. The result is more efficient delivery of rimpull for production. These controls also improve the ride quality of the machine.
We’ve improved oil flow to the output gear group for long term durability, and you’ll change the oil every 1,000 hours reducing maintenance time and cost.
Axles
Our axles have grown to manage the added weight and capacity of the machine. We’ve increased the axle housing thickness for abrasion protection and corrosion resistance. There has been a slight track width increase of 64 mm (2.51 in) with these new axles. The R1700 has the same differential used on our R2900 machine. Here are the major updates to the axle:
Larger spindles.
Wider planetary gear.
Larger dual cone seal.
Upgraded planet shaft retention.
Larger trunnions and trunnion supports and trunnion bearings.
Electro-Hydraulic Braking
Adding EH braking allowed us to substantially improve the traction control system, engine overspeed limiting, ground speed limiting and improved braking under remote control.
Hydraulics
Next Generation Power, Performance and Safeguards
Our hydraulic system on this machine is state-of-the-art. It uses on-demand piston pumps for durability, higher pressures and overall system efficiency. Full system pressure is available to the operator while the engine is at idle. The system is load sensing, and it puts priority on braking and steering for safety.
During loading – it is providing significantly more breakout force during digging and at the other end of the cycle we’ve given the machine faster dumping times. The front linkage cylinders have been repositioned for better mechanical lift.
The system also has some built in safeguards. Should the operator open the door to the cab while the machine is energized, the hydraulic system is neutralized and implements will not move.
Operators will appreciate the responsiveness of the machine.
During the load or dump cycle – the harder the operator pushes the controls, the faster the machine responds.
For the first time, we can offer automated loading of the bucket with the Auto Dig feature. This is a system that is well proven on Cat surface products, and it paves the way for full autonomy in the future.
The steering system is pilot controlled to provide more acute feel for the operator as they maneuver in tight places.
Ride control is now fully integrated into the hydraulic system and engages automatically as the machine goes above 5 km/h (3 mph). We are electronically snubbing the cylinders for protection and operator comfort.
The R1700 has auto retarding that is hydraulically actuated.
As the name implies, the system comes on automatically when the operator’s foot is lifted from the throttle.
It will improve cycle times as operators gain confidence and become more comfortable on downhill grades at faster speeds.
Operator Environment
Next Generation Control, Information, Comfort and Safety
The cab on the R1700 maintains the same footprint as previous generations; however, we have completely changed the interior with new space allotment for the operator and all new electronic components. Material has been added to the underside of the cab structure to protect against corrosion. We offer both an enclosed cab or an open cab configuration.
Operator Comfort
Additional space created around the operator.
New, adjustable padding for the operator’s knees.
The operator sits slightly lower inside the cab for improved ride quality and head room.
Additional space created for foot comfort when operating the pedals.
Climate control standard with enclosed cab option.
All new HVAC coverage with improved airflow, greater defrosting coverage, and reduced noise levels.
Improved ergonomics on all controls, joy sticks.
Adjustable arm rest.
Cab is isolation mounted to reduce vibration transfer to the operator.
Optional dual pane windows reduce noise and improve temperature control in extreme ambient conditions.
Cab pressurization to keep dust out.
Automatic loading of the bucket reduces fatigue.
Two air ride seat options – with the Tee seat allowing for personal protective equipment.
Ride control option with electronic cylinder snubbing.
New cup holder.
Operator Safety
Operator present system and door latch sensor.
Dual secondary emergency exits.
Dual zipper sealed glass standard.
Significantly improved HVAC double ducting to defrost and dehumidify glass.
Increased door width.
EROPS/OROPS certified.
Twin windshield wipers on the forward-facing window and single wipers on the door and rear facing window.
Camera for operating in reverse with color display.
Fire Suppression activation from within the cab.
Caterpillar designed, new remote control with full diagnostics display.
Ground speed control limiting can be set from the factory.
Neutral coast inhibiting.
Information Displays and Technology
Real time system information on high resolution dash display with 11 language options.
Tire pressure monitoring.
Dash display is quick-start enabled with information available before engine start.
Operator can see that the lock-up clutch, ride control, auto loading and high beam lights are in use, and that regeneration emission controls are engaged.
J1939 and Ethernet communications connectivity available.
Product Link™ Elite (PLE) data analysis with WiFi connectivity.
All machine ECMs have been moved to a dedicated sealed box outside of the cab.
Command for Underground now managed through onboard electronics and available automation-ready from the factory.
Electrical Systems
Long Term Reliability and Corrosion Resistance
Cat electrical components – like connectors, wiring harnesses and ECMs – are a critical element in our machine’s long-term reliability. Our electrical components are designed to live in corrosive environments.
For the R1700, we have placed all the machine’s ECMs in a single, air cooled and sealed box located on the service platform of the machine. This allowed us to provide clean, simplified electrical routings throughout the machine and greatly improved access and convenience for service personnel.
Other key electrical components include a new high-resolution camera system – with three new cameras added for Command for Underground.
For this machine, Caterpillar has standardized on LED lights, with plenty of illumination both to the front and rear of the machine.
We added a cab door-mounted light to provide visibility to the walls when turning.
The transmission bay has a light that is actuated on the side of the cab.
A green light at the back of the cab indicates remote control is being activated.
Two amber lights indicate the machine is operating under remote control.
An optional truck loading light is available – it comes on automatically as the lift arms reach 50 percent of their travel up.
For safety – we have placed the electrical control box at ground level on the cold side of the engine and we’ve improved battery accessibility also from ground level.
One of the more significant improvements we’ve made to our electrical components is incorporating Command for Underground into our ECMS. This allows us to deliver the technology ready from the factory.
Payload monitoring is available and requires only low lift of the bucket to take the measurement.
Buckets and Ground Engaging Tools
Performance Has Never Been Better
Caterpillar designed and manufactured the R1700 bucket to match its performance capabilities. The result is a newly patented bucket design with the following advantages:
Load path management for long wear life.
Increased throat angle for easier loading in rock.
Improved tire coverage for cleanup and tire protection.
Added strength to match improved break out force.
Added stiffness to inside torque tube for torsional rigidity.
Corner gussets on top.
There are five bucket sizes ranging from 5.7 m³ (7.5 yd³) up to 8.6 m³ (11.2 yd³).
Complimenting this bucket design is a new Ground Engaging Tool offering. The Bolt-On, Half Arrow GET (BOHA) underwent rigorous field testing prior to production. The advantages of this system are:
A reduction in throw away material since there is no welding or cutting.
Integrated lift eyes make the segments easy to handle.
Built-in wear indicators allow you to plan downtime for replacement.
Replacement is simple, quick, and allows your machine to go back into production in less time. In one field trial instance – a customer saw a 75 percent reduction in downtime to replace their GET and 39 percent reduction in their cost per hour.
Safety
Always Top of Mind, Always the Priority
We’ve taken safety to another level on the R1700. Critical new features include:
Dedicated fire suppression canister real estate and factory available.
Multiple fire suppression activation points.
Newly redesigned handrail system with full coverage for people on the work platform.
Operator present system with hydraulic system neutralization and door sensor.
Anti-slip tread on all walking surfaces.
Improvements in visibility, lighting coverage and camera coverage.
New braking performance, slope holding capabilities, brake wear indicators.
Ground level access to most daily service checks.
Service area located on cold side of engine.
Thermal protection on aftertreatment components.
Integrated lock out/tag out points.
In cab warnings – both visual and audible.
Cat line of site console has new ergonomics, emergency shut down and fire suppression activation control.
Front linkage pins for locking the lift arms in place.
Reverse alarm.
Bolt-on tow hook.
Tire pressure monitoring system.
Serviceability – Introducing Modular Service Components
Modular Components
The R1700 features several components – like the HVAC system and the cooling system – as modular designs that can be removed from the machine as a single unit and slotted back into place as a single unit allowing the machine to get back into service much quicker. Similarly, all machine ECMs are in a single, well protected and sealed box accessible from the work platform.
Service Access
In addition to modular components, all filter and key service tasks have been grouped into a centralized service section on the cold side of the engine. The radiator guard swings open for ground-level access to the radiator, and oil coolers and the batteries are easily accessed just under the centralized service location.
Machine Health Information
Critical machine information is now visible on an integrated display when operating the machine using the Cat line-of-sight remote control console.
In cab health monitoring can be viewed on the digital display and monitored through the Cat Product Link Elite (PLE) system formerly known as VIMS.
The fuel tank is easily cleaned or replaced if damaged as it bolts in to the frame.
Lubrication options are available fitted from the factory.
Our new brake release and tow hook option allows you to remove the machine and disengage the park brake in the event the machine must be towed.
Technology Enabled Solutions
MineStar™ and Command for Underground
Caterpillar’s technology suite for mining operations is called MineStar. An important element of MineStar for our underground mining customers is Command for Underground. This technology enabled solution allows you to take a stepped approach to full autonomy.
Command for Underground has been proven to significantly increase production by doing a great deal more than just reducing exposure to hazardous conditions. Using our new, ergonomically correct operator console, your team can operate your fleet of LHDS from a safe environment either above or below ground.
Command for underground can increases productivity in several ways:
Improved comfort and safety leads to more confident and productive operators.
Safety is enhanced through locating the operator in an ergonomic and isolated environment where he can maintain high productivity rates. From here the operator can run either one or multiple machines based on the system selected.
Damage from impacts with drive walls and subsequent downtime can be eliminated using our guidance system.
Shift changes are a simple matter of getting up off the console chair – and having the next person sit down. There’s no need for your LHD operator to take up space in the elevator, or take the time to chase down a machine inside the mine.
Thanks to the R1700, MineStar and Command for Underground are ready for a new, more advanced phase – complete automation. We’ve made adopting this new technology even easier by making the machine technology enabled right from the factory.
The R1700 is the first Cat LHD to be able to offer all the following technology enabled solutions:
Line of sight remote – with newly redesigned remote control.
Tele remote operation – where the operator is not within sight of the machine.
Guidance – is a means of tele remote operation that does not rely on the operator to avoid collisions with walls.
Co-Pilot – only requires directional input from the operator (forward or reverse) – self steering is done with map guidance.
Fully Autonomous operation – is made possible on the R1700 with the addition of three new controls:
Auto Pilot – oversees tramming of the machine without input between the load and dump points.
Auto Dump – allows the machine to dump into a fixed infrastructure without operator input.
Auto Dig – is autonomous digging and bucket loading that is now available on the R1700.
The R1700 also has higher tramming speeds while operating the machine in autonomous modes – allowing the machine to reduce cycle times and improve productivity.
Manufacturing
A Focus on Quality and Safety
The R1700 is designed in Burnie Tasmania (Australia) and manufactured in Rayong Thailand.
Burnie is also home of the Caterpillar Burnie Proving Grounds where a complete Command for Underground test facility and training center is available to customers. A video of this facility is available at www.cat.com/underground.
The Caterpillar factory in Rayong is one of the newest manufacturing facilities at Caterpillar, with 100 percent focus given to underground hard rock mining products.
The Rayong facility was designed and built by Caterpillar, and is managed and operated by a highly skilled and uniquely diverse team who have embedded the Cat Production System into their culture.
Upon joining the team in Rayong, an employee will undergo 250 hours of training before performing their task on the line. Significantly more education is given to our welders. To ensure they succeed in their tasks, we provide our welders with the latest tooling so that our team can work ergonomically and achieve the weld penetration specified. The quality of your Cat machine starts with this team.
Each step of the manufacturing process has quality control gates, and every single employee is empowered to stop the assembly line to continuously improve safety or the manufacturing process.
A clean environment helps keep components free of contaminants and provides a better work climate. Like all Caterpillar facilities around the world, visitors are most welcome to see where and how their machines are made.
Product Parameter
Overview
Our goal for the redesign of the R1700 was simple; add value, power and performance with safety at its core. With each cycle, the R1700 hauls 20 percent more payload, it loads, climbs, hauls and dumps quicker. It features three engine emission options that can be tailored to your mine’s ventilation requirements. The R1700 is a powerful new tool for mining.
Engine
Units:
Engine Model | Cat® C13 Cat® C13 | More |
Gross Power - VR Engine - ISO 14396 | 361.0 HP 269.0 kW | More |
Rated Power: Gross Power - Equivalent to U.S. EPA Tier 3/EU Stage IIIA | 361.0 HP 269.0 kW | More |
Rated Power: Gross Power - ISO 14396 - Ventilation Reduction (VR) | 361.0 HP 269.0 kW | More |
Rated Power: Gross Power - ISO 14396 - Stage V | 345.0 HP 257.0 kW | More |
Operating Specifications
Nominal Payload Capacity | 33069.0 lb 15000.0 kg | More |
Gross Machine Mass - Loaded | 138737.0 lb 62930.0 kg | More |
Static Tipping Load - Straight Ahead - Lift Arms Horizontal | 82043.0 lb 37214.0 kg | More |
Static Tipping Load - Full Turn - Lift Arms Horizontal | 68939.0 lb 31270.0 kg | More |
Breakout Force - Lift and Tilt | 53330.0 lb 24190.0 kg | More |
Rated Payload | 33069.0 lb 15000.0 kg | More |
Weights
Empty - Front Axle | 37871.0 lb 17178.0 kg | More |
Empty - Rear Axle | 56370.0 lb 25569.0 kg | More |
Loaded - Front Axle | 90928.0 lb 41244.0 kg | More |
Loaded - Rear Axle | 36383.0 lb 16503.0 kg | More |
Transmission
Forward - 1 | 3.0 mile/h 4.9 km/h | More |
Forward - 2 | 5.7 mile/h 9.2 km/h | More |
Forward - 3 | 10.2 mile/h 16.4 km/h | More |
Forward - 4 | 17.9 mile/h 28.8 km/h | More |
Reverse - 1 | 3.7 mile/h 5.9 km/h | More |
Reverse - 2 | 6.5 mile/h 10.5 km/h | More |
Reverse - 3 | 11.6 mile/h 18.7 km/h | More |
Reverse - 4 | 20.2 mile/h 32.5 km/h | More |
Hydraulic Cycle Times
Raise | 6.8 s 6.8 s | More |
Dump | 3.3 s 3.3 s | More |
Lower, Empty, Float Down | 2.9 s 2.9 s | More |
Total Cycle Time | 13.2 s 13.2 s | More |
Bucket Capacities
Bucket Capacities | 5.7-8.6 m³ (7.5-11.2 yd³) 5.7-8.6 m³ (7.5-11.2 yd³) | More |
Dump Bucket - 1 - Standard Bucket | 7.5 yd³ 5.7 m³ | More |
Dump Bucket - 2 | 8.0 yd³ 6.1 m³ | More |
Dump Bucket - 3 | 8.6 yd³ 6.6 m³ | More |
Dump Bucket - 4 | 9.8 yd³ 7.5 m³ | More |
Dump Bucket - 5 | 10.5 yd³ 8.0 m³ | More |
Light Material Bucket | 11.2 yd³ 8.6 m³ | More |
Ejector Bucket | 7.6 yd³ 5.8 m³ | More |
Turning Dimensions
Outside Clearance Radius | 270.0 in 6857.0 mm | More |
Inner Clearance Radius | 123.5 in 3139.0 mm | More |
Axle Oscillation | 8° 8° | More |
Articulation Angle | 44° 44° | More |
Tires
Tire Size | 26.5R25 26.5R25 | More |
Service Refill Capacities
Cooling System | 19.8 gal (US) 75.0 l | More |
Engine Crankcase | 9.8 gal (US) 37.0 l | More |
Hydraulic Tank | 35.7 gal (US) 135.0 l | More |
Service Capacities - Not Refill
Fuel System | 128.4 gal (US) 486.0 l | More |
DEF Tank | 7.1 gal (US) 27.0 l | More |
Front Differential and Final Drive | 27.4 gal (US) 104.0 l | More |
Rear Differential and Final Drive | 27.7 gal (US) 105.0 l | More |
Transmission | 14.2 gal (US) |