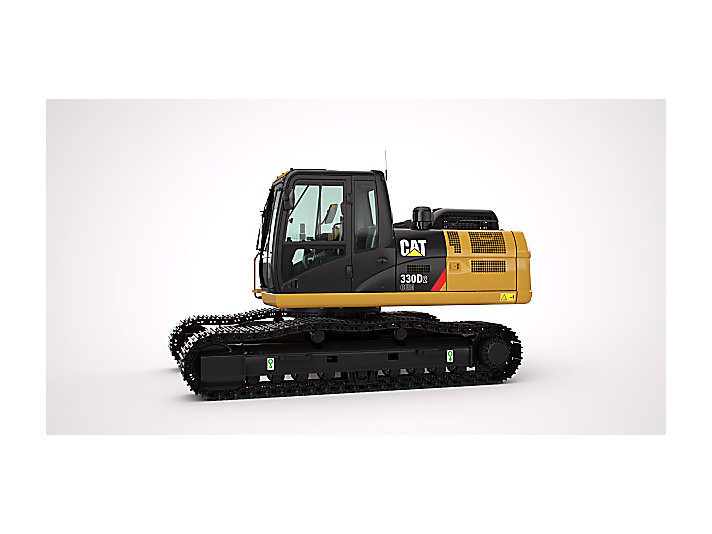
Cat Frontless Excavators 330D2 L OEM
Product Feature
Complete Customer Support
Product Support
You can maximize your machines' uptime with the Cat worldwide dealer network. You can also decrease your repair costs by utilizing Cat remanufactured components while contributing to sustainable development.
Machine Selection
What are the job requirements and machine attachments? What production do you need? Your Cat dealer can provide recommendations to help you make the right machine configuration.
Purchase
You can ensure lower owning and operating costs by utilizing unique Cat dealer services and financing options.
Customer Support Agreements
Cat dealers offer a variety of customer support agreements and work with you to develop a plan to meet your specific needs. These plans can cover the entire machine, including attachments, to help protect your investment.
Operation
You can boost your profits by improving your operators' techniques. Your Cat dealer has videos, literature, and other ideas to help increase productivity. Caterpillar also offers simulators and certified operator training to help maximize the return on your investment.
Replacement
Repair, rebuild, or replace? Your Cat dealer can help you evaluate the cost involved so you can make the best choice for your business.
Service and Maintenance
Ground-Level Service
The design and layout of the 330D2 L was made with the service technician in mind. Most service locations are easily accessible at ground level to allow service and maintenance to get completed quickly and efficiently.
Air Filter Compartment
The air filter features a double-element construction for superior cleaning efficiency. When the air cleaner plugs, a warning is displayed on the monitor screen inside the cab.
Pump Compartment
A service door on the right side of the upper structure allows ground-level access to the pump, pilot filter, engine oil filter and water separator with primary fuel filter.
Radiator Compartment
The left rear service door allows easy access to the engine radiator, oil cooler, air-to-air-aftercooler, water separator, second and third fuel filters, and fuel cooler. A reserve tank and drain cock are attached to the radiator for simplified maintenance.
Greasing Points
Conveniently located grease blocks help you get lube in hard-to-reach places, making routine boom, stick, and bucket linkage maintenance quick and easy.
Fan Guard
The engine radiator fan is completely enclosed by fine wire mesh, reducing the risk of an accident.
Anti-Skid Plate
Anti-skid plate covers top of storage box and upper structure to prevent slipping during maintenance.
Diagnostics and Monitoring
The 330D2 L is equipped with S∙O∙SSM ports to easily sample hydraulic and engine oil quality. Test ports are also conveniently located so you can test coolant and hydraulic pressure.
Optioinal Undercarriage and Structures
Robotic Welding
Up to 95% of the structural welds on a Cat Excavator are completed by robots. Robotic welds achieve over three times the penetration of manual welds.
Carbody Design and Track Roller Frames
X-shaped, box-section carbody provides excellent resistance to torsional bending. Robot-welded track roller frames are press-formed, pentagonal units which deliver exceptional strength and service life.
Rollers and Idlers
Sealed and lubricated track rollers, carrier rollers, and idlers provide excellent service life, to keep the machine in the field longer.
Long Undercarriage
The long undercarriage (L) maximizes stability and lift capacity. This long, wide and sturdy undercarriage offers a very stable work platform.
Tracks
The 330D2 L track links are assembled and sealed with grease to decrease internal bushing wear, reduce travel noise and extend service life lowering operating costs.
Counterweights
The 5.9 mt (6.5 t) standard weight makes a better choice for heavy lifting with long undercarriage. Counterweights are bolted directly to the main frame for extra rigidity.
Operator Station
ROPS Certified Operator Station
The 330D2 L features a ROPS (Roll Over Protective Structure) compliant cab structure as standard which meets OSHA and MSHA sound requirements. This design also allows for a Falling Object Guard System (FOGS) or front windshield guard to be bolted directly to the cab, either at the factory or in the field, enabling the machine to meet all job site requirements.
Monitor
The new monitor features a 40 percent larger screen than the previous model's and is equipped with a warning lamp and buzzer for critical engine oil pressure, coolant temperature and oil temperature. Programmable in up to 42 languages, the monitor clearly displays critical information including filters and fluid change intervals and the image from the optional rearview camera, enhancing job site productivity and safety.
Seat
The suspension seat provides a variety of adjustments to accommodate a wide range of operators. All seats include a reclining back, upper and lower seat slide adjustments, and height and tilt adjustments.
Controls
Operators can adjust the right and left joysticks for individual preferences, helping them become more comfortable, more productive, and more alert. Low-effort pilot-operated joystick controls are designed to match your natural wrist and arm position for maximum comfort and minimum fatigue.
Climate Control
The 330D2 L offers positive filtered ventilation with a pressurized cab. Fresh air or recirculated air can be selected, which makes working in the heat and cold much more pleasant.
Cab Structure and Mounts
The cab shell is attached to the frame with viscous rubber cab mounts which dampen vibrations and sound levels while enhancing operator comfort. Thick steel tubing along the bottom perimeter of the cab improves resistance to fatigue and vibration.
Key Features
Performance/Efficiency
Up to a 15% reduction in fuel consumption
Improves fuel efficiency by managing pump and isochronous engine speed control
The Cat C7.1 engine meets EPA Tier 3 and EU Stage III emission regulations (for 2015) sound regulations
Electrical Fuel Priming Pump (EPP) replaces hand priming pump
Pressure sensor measures Negative Flow Control pressure to improve the hydraulic efficiency
Ease of Operation
Ergonomically designed cab with easy to operate controls
Multiple seat and joystick adjustment options enhance comfort
Excellent work site visibility from the cab enhances productivity
Optimized low effort joystick controls reduces operator fatigue
New monitor with 40% larger viewing screen, 4× higher resolution and 42 language options available
Reliability/Serviceability
The strong and durable carbody has been designed to work in the toughest operating conditions
All electrical wires are colored, numbered and protected with thick braiding for ease of identification and long life
Heavy duty stress-relieved booms and heavy duty sticks are standard
Grease and Lubricated Tracks (GLT) provides longer life
New fuel injection system for improved reliability
Reduced Costs
The machine has improved filtration efficiency and system robustness
The machine service interval is 500 hours
There are two different power modes; High Horse Power (HHP) and ECO Mode. ECO Mode reduces fuel consumption up to 15% with no loss in digging or lifting forces
Technology
Integrated Cat technology solutions increase production and minimize operating costs
Product Link™ reports key information from the machine to any location
New Appearance
The 330D2 L machine has a stylish modern look
Integrated Technologies
Cat Connect makes smart use of technology and services to improve your job site efficiency. Using the data from technology-equipped machines, you'll get more information and insight into your equipment and operations than ever before. Cat Connect technologies offer improvements in these key areas: Equipment Management – increase uptime and reduce operating costs. Productivity – monitor production and manage job site efficiency. Safety – enhance job site awareness to keep your people and equipment safe.
Cat Connect LINK Technologies
LINK technologies wirelessly connect you to your equipment giving you access to essential information you need to know to run your business. Link data can give you valuable insight into how your machine or fleet is performing so you can make timely, fact-based decisions that can boost job site efficiency and productivity.
Product Link/VisionLink®
Product Link is deeply integrated into your machine, helping to take the guesswork out of equipment management. Easy access to timely information like machine location, hours, fuel usage, idle time and event codes via the online VisionLink user interface can help you effectively manage your fleet and lower operating costs.
Cat Connect DETECT Technologies
DETECT technologies combine safety features, functionalities and alerts to enhance your job site awareness and keep your people and assets safe.
Rearview Camera
Rear vision cameras greatly enhance visibility behind the machine, helping the operator work more safely and productively. The camera view is automatically displayed on the integrated in-cab monitor increasing awareness of the working area around the machine giving the operator the confidence to work more safely and efficiently, at maximum potential.
Hydraulics
Hydraulic System
Hydraulic system pressure from the two-hydraulic pump system delivers terrific digging performance and productivity.
Pilot System
An independent pilot pump enables smooth, precise control for the front linkage, swing, and travel operations.
Hydraulic Activation Control Lever
With the hydraulic activation lever in the neutral position, all front linkage, swing, and travel functions are isolated.
Component Layout
The hydraulic system and component locations have been designed to provide a high level of system efficiency. The main pumps, control valves, and hydraulic tank are located close together to allow for shorter tubes and lines between components, reducing friction loss and pressure drops.
Hydraulic Cross-Sensing System
The hydraulic cross-sensing system utilizes each of two hydraulic pumps to 100 percent of engine power under all operating conditions. This improves productivity with faster implement speeds and quicker, stronger pivot turns.
Engine
Reliable Cat C7.1 Engine
The Cat C7.1 engine has been designed to meet EPA Tier 3 and EU Stage III emission regulations. The C7.1 engine incorporates proven, robust components and precision manufacturing you can count on for reliable and efficient operation. This is a proven engine that boasts improved reliability, as it's less sensitive to low quality fuel and also delivers reduced fuel consumption. An ECO-Mode feature helps to reduce fuel consumption by up to 15 percent for fuel-conscious customers with no loss in digging or lifting forces.
Automatic Engine Control
Automatic engine control is activated during no-load or light-load conditions which reduces engine speed to minimize fuel consumption.
Air Cleaner
The radially sealed air filter features a double-layered filter core for more efficient filtration and is located in a compartment behind the cab. A warning is displayed on the monitor when dust accumulates above a preset level.
Filtration System
The C7.1 engine features an improved filtration system to ensure good reliability to fuel injection system components. Intervals have been extended and the number of filters has been increased to 3. The primary filter and the secondary twin filters improve filtration efficiency and machine robustness.
Product Parameter
Overview
The 330D2 L OEM comes with a number of new developments and features to help you make the best use of your machine. Isochronous engine speed control, a new fuel filtration system, a built-in economy mode to save up to a 15% fuel consumption and energy. A variable speed fan with viscous clutch makes this machine productive, efficient and safe.
Engine
Units:
Engine Model | Cat® C7.1 | Cat® C7.1 |
Net Flywheel Power | 209.0 HP | 156.0 kW |
Bore | 4.13 in | 105.0 mm |
Stroke | 5.31 in | 135.0 mm |
Displacement | 428.0 in³ | 7.1 l |
Engine Power - ISO 14396 | 213.0 HP | 159.0 kW |
High Idle Speed | 1700.0 r/min | 1700.0 r/min |
Low Idle Speed | 950.0 r/min | 950.0 r/min |
Maximum Altitude - With Derate | 16404.0 ft | 5000.0 m |
Maximum Altitude - Without Derate | 9842.0 ft | 3000.0 m |
Maximum Torque - Torque Peak - At 1,400 rpm | 663.8 lb/ft | 900.0 N·m |
Net Power - SAE J1349/ISO 9249 | 209.0 HP | 156.0 kW |
Rated Speed - Engine | 1800.0 r/min | 1800.0 r/min |
Type | Direct Injection | Direct Injection |
Note | The C7.1 engine meets EPA Tier 3, EU Stage III emission regulations. | The C7.1 engine meets EPA Tier 3, EU Stage III emission regulations. |
Weights
Frontless Weight | 51700.0 lb | 23450.0 kg |
Maximum Operating Weight* | 66970.0 lb | 30375.0 kg |
Note | *Dependent on application, Review | *Dependent on application, Review |
Service Refill Capacities
Fuel Tank Capacity | 137.4 gal (US) | 520.0 l |
Cooling System | 8.2 gal (US) | 31.0 l |
Engine Oil | 5.8 gal (US) | 22.0 l |
Swing Drive | 2.6 gal (US) | 10.0 l |
Final Drive - Each | 1.6 gal (US) | 6.0 l |
Hydraulic System - Including Tank | 81.9 gal (US) | 310.0 l |
Hydraulic Tank | 67.9 gal (US) | 257.0 l |
Swing Mechanism
Swing Speed | 9.6 r/min | 9.6 r/min |
Swing Torque | 60627.6 lb/ft | 82.2 kN·m |
Drive
Maximum Drawbar Pull | 55752.6 lbf | 248.0 kN |
Maximum Travel Speed | 3.4 mile/h | 5.3 km/h |
Hydraulic System
Main System - Maximum Flow at Operation (1,700 rpm) - Each | 240 × 2 (480 total) L/min [63.4 × 2 (126.8 total) gal/min] | 240 × 2 (480 total) L/min [63.4 × 2 (126.8 total) gal/min] |
Main System - Maximum Flow at Travel H/L (1,800 rpm) | 254 × 2 (508 total) L/min [67.1 × 2 (134.2 total) gal/min] | 254 × 2 (508 total) L/min [67.1 × 2 (134.2 total) gal/min] |
Main System - Maximum Flow at Travel L/L (1,750 rpm) | 247 × 2 (494 total) L/min [65.2 × 2 (130.4 total) gal/min] | 247 × 2 (494 total) L/min [65.2 × 2 (130.4 total) gal/min] |
Maximum Pressure - Equipment | 5076.4 psi | 35.0 MPa |
Maximum Pressure - Swing | 3982.7 psi | 27.5 MPa |
Maximum Pressure - Travel | 5076.4 psi | 35.0 MPa |
Pilot System - Maximum Flow | 6.1 gal/min | 23.1 l/min |
Pilot System - Maximum Pressure | 568.6 psi | 3920.0 kPa |
Swing System - Maximum Flow | 63.4 gal/min | 240.0 l/min |
Standards
Brakes | SAE J1026/APR90 | SAE J1026/APR90 |
Cab/FOGS | SAE J1356 FEB88; ISO 10262 | SAE J1356 FEB88; ISO 10262 |
Cab - ROPS | ISO 12117-2:2008 | ISO 12117-2:2008 |
Sound Performance
ISO 6395 - Spectator Noise | 104.0 dB(A) | 104.0 dB(A) |
ISO 6396 - Operator Noise (Closed) | 71.0 dB(A) | 71.0 dB(A) |