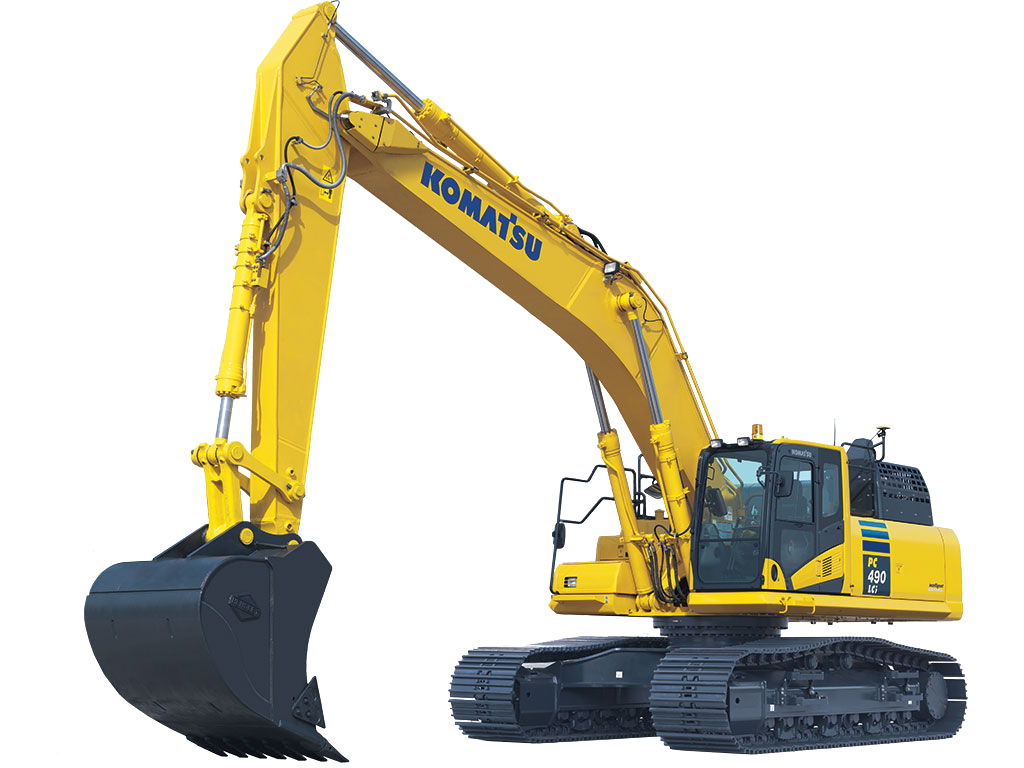
Komatsu PC490LCi-11 LARGE EXCAVATORS
Product Feature
Auto Grade Assist
With the auto grade assist function, the operator moves the arm, the boom adjusts the bucket height automatically, tracing the target surface and minimizing digging too deep. This allows the operator to perform rough digging without worrying about the design surface, and to perform fine digging by operating the arm lever only. The working range is expanded by holding the lever to move the boom downward.
Auto Stop Control
During boom or bucket operation, the work equipment automatically stops when the bucket edge reaches the design surface, thus minimizing damage to the design surface.
Facing Angle Compass
The orientation and color of the facing angle compass’s arrow shows the operator the facing angle of the bucket edge relative to the target surface. This allows the bucket edge to be accurately positioned square with the target surface, which is useful when finishing slopes.
Komatsu intelligent Machine Control Components
Standard factory installed intelligent Machine Control system for 3D GNSS machine guidance and semi-automatic control. Sensor package includes stroke sensing hydraulic cylinders, inertial measurement units, and GNSS antennas.
intelligent Machine Control
World’s first intelligent Machine Control excavator with semi-automatic control allows the operator to improve work efficiency as compared to conventional aftermarket machine guidance (indicate only) or manual operation. Rough digging to finish grading, intelligent Machine Control minimizes over-excavation to make every pass count.
Minimum Distance Control
The intelligent Machine Control excavator controls the bucket by automatically selecting the point on the bucket closest to the target surface. Should the machine not be facing a sloped surface at a right angle, it will still follow the target surface and minimize digging below it.
Control Box
The monitor of the Komatsu intelligent Machine Control (control box) uses a large 12.1" (30.7 cm) touch screen for visibility and ease of use. The screen layout is customizable to display information in an easily understood fashion with a variety of views including 3D, plan, and section.
Stroke Sensing Hydraulic Cylinder
Sensor package with stroke sensing hydraulic cylinders provides real time position, immediately displayed to the operator. This is in contrast to conventional aftermarket machine guidance (indicate only) systems with tilt sensors that require time to stabilize.
Product Parameter
Fuel tank | 650 ltr | 172 U.S. gal |
Coolant | 47 ltr | 12.4 U.S. gal |
Engine | 38 ltr | 10.0 U.S. gal |
Final drive, each side | 11 ltr | 2.9 U.S. gal |
Swing drive | 20 ltr | 5.3 U.S. gal |
Hydraulic tank | 248 ltr | 65.5 U.S. gal |
Diesel Exhaust Fluid (DEF) tank | 39 ltr | 10.3 U.S. gal |
Steering control | Two levers with pedals | |
Drive method | Hydrostatic | |
Maximum drawbar pull | 329 kN / 33510 kg | 73,880 lb |
Gradeability | 35° | 70% |
Maximum travel speed: (Auto-Shift): | ||
High | 5.5 km/h | 3.4 mph |
Mid | 4.2 km/h | 2.6 mph |
Low | 3.0 km/h | 1.9 mph |
Service brake | Hydraulic lock | |
Parking brake | Mechanical disc brake |
Model | |
Komatsu SAA6D125E-7* |
Type | |
Water-cooled, 4-cycle, direct injection |
Aspiration | |
Komatsu Variable Geometry Turbocharger with air-to-air aftercooled EGR |
Number of cylinders | |
6 |
Bore | 125 mm | 4.92" |
Stroke | 150 mm | 5.91" |
Piston displacement | 11.04 ltr | 674 in³ |
Horsepower | |
|
SAE J1995 : Gross | 270 kW | 362 HP |
ISO 9249/SAE J1349 : Net | 268 kW | 359 HP |
Rated rpm | |
1900 rpm |
Governor | |
All-speed control, electronic. |
Fan drive method for radiator cooling | |
Hydraulic |
*EPA Tier 4 Final emissions certified | |
|
Main pump: | ||
Pumps for | Boom, arm, bucket, swing, and travel circuits | |
Type | Variable displacement axial piston type | |
Maximum flow | 780 ltr/min | 206 U.S. gal/min |
Hydraulic motors: | ||
Travel | 2 x axial piston motor with parking brake | |
Swing | 1 x axial piston motor with swing holding brake | |
Relief valve setting: | ||
Implement circuits | 380 kgf/cm²/ 37.3 MPa | 5,400 psi |
Travel circuit | 380 kgf/cm² / 37.3 MPa | 5,400 psi |
Swing circuit | 285 kgf/cm²/ 27.9 MPa | 4,050 psi |
Pilot circuit | 33 kgf/cm² / 3.2 MPa | 470 psi |
Hydraulic cylinders: | ||
Number of cylinders | Bore x Stroke x Rod Diameter | Bore x Stroke x Rod Diameter |
Boom / 2 | 160 mm x 1570 mm x 110 mm | 6.3" x 61.8" x 4.3" |
Arm / 1 | 185 mm x 1820 mm x 120 mm | 7.3" x 71.7" x 4.7" |
Bucket / 1 | 160 mm x 1270 mm x 110 mm | 6.3" x 50" x 4.3" |
Fixed Gauge | ||
Shoes | 700 mm | 28" |
Operating Weight | 47930 kg | 105,670 lb |
Ground Pressure | 0.73 kg/cm² | 10.38 psi |
Shoes | 800 mm | 31.5'' |
Operating Weight: | 48430 kg | 106,770 lb |
Ground Pressure | 0.65 kg/cm² | 9.20 psi |
Shoes | 900 mm | 35.5" |
Operating Weight: | 48920 kg | 107,850 lb |
Ground Pressure | 0.58 kg/cm² | 8.32 psi |
Drive method | Hydrostatic motor |
|
Swing reduction | Planetary gear | |
Swing circle lubrication | Grease-bathed | |
Service brake | Hydraulic lock | |
Holding brake/Swing lock | Mechanical disc brake | |
Swing speed | 9.0 rpm | |
Swing torque | 13414 kg•m | 97,024 ft. lbs. |
Center frame | X-frame |
Track frame | Box-section |
Track type |
Sealed |
Track adjuster | Hydraulic |
Number of shoes | 49 each side |
Number of carrier rollers |
2 each side |
Number of track rollers | 8 each side |