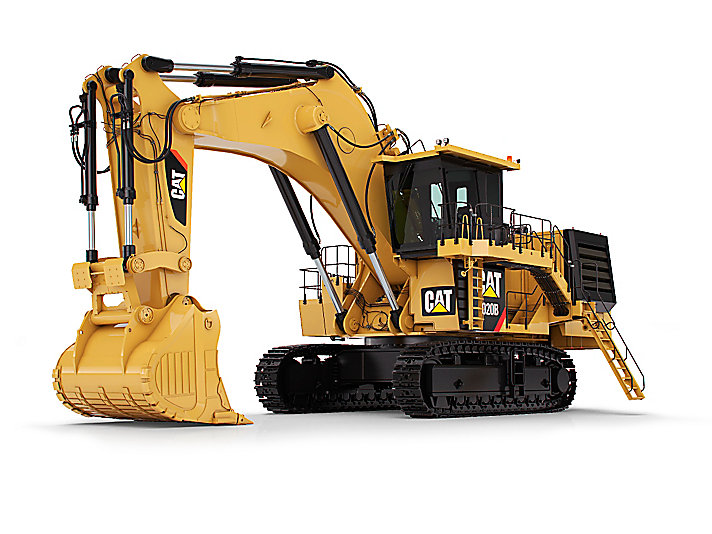
Cat Hydraulic Mining Shovels 6020B
Product Feature
State-of-the-Art Operator’s Cab – Protecting and Supporting Your Most Important Asset: the Operator
Optimizing Operator Situational Awareness with Class-leading Cab Visibility
Direct view of tracks, while seated in the operator's station, via floor window for safe and easy machine repositioning and underfoot obstacle avoidance.
Safe machine positioning and truck loading via large windshield and side windows.
Multiple strategically positioned and high-powered LED lights for maximum illumination of the digging area in dark conditions.
Heavy-duty wiper ensures good visibility in inclement weather conditions.
Supporting Peak Operator Performance with Enhanced Training Capability
First in class and patented three-seat design with unobstructed view of digging environment from all seats.
Elevated observer’s work station, positioned behind the operator seat, provides space for a laptop and great visibility of the operator station and the digging environment.
Dual in-cab emergency stop buttons easily accessible from both trainer seats and operator station.
Maximizing Operator Alertness and Effectiveness with Leading Comfort Features
Extremely quiet and fully pressurized cab environment.
Ergonomic operator seat and controls with armrest adaptable to operator preference.
10 inch touch-screen display includes troubleshooting aids and machine documentation.
Extensive in-cab air distribution via powerful HVAC unit and multiple, optimally positioned, vents.
Cab module supported with rubber mounts for shock absorption.
Electro-servo control system ensures no hydraulic lines are present in the cab for a clean, quiet, and odorless environment.
Adaptive Hydraulic System – Reliable Performance from an Efficient, Clean, and Serviceable System
The revolutionary Adaptive Hydraulic System combines industry-leading and patent-pending dedicated pump-flow allocation technology with proven Cat features like independent oil cooling and boom float to generate flow and pressure, without waste – providing a 20% fuel efficiency advantage.
Dedicated Pump-flow Allocation Technology
There are six main pumps, comprised of three identical double pumps, supply cylinders, travel motors and swing motors. Each of these main pumps can be used for any cylinder function, with priority to swing and travel.
Pump flow of each circuit is directly controlled by the position of the joystick, which maximizes the hydraulic efficiency of the engine and dramatically reduces load factors.
No oil flow must be throttled
No high-pressure oil is returned to the tank
Pump flow allocation can be supplied simultaneously to independent circuits (functions) or summarily for a single circuit (function), which enables the operator to directly control the speed of each function.
More precise digging of slopes and trenches, especially on construction sites
Faster cylinder speeds on production mine sites
Independent Cooling System
The return oil cooling system is fully independent from the engine cooling system
Cooler system temperatures extend component life
Boom Float
During boom lowering, the float feature reduces engine demand
Regeneration of boom oil increases energy efficiency
Serviceability
Reduced load factors and efficiency gains are the basis for longer component life expectancies
Hydraulic value block is mounted on the boom, providing easier access for service
Consistent Oil Cleanliness for Dependable Hydraulic System Performance
The hydraulic system design has been optimized for peak performance and reliability.
Machine comes equipped with standard high-pressure and return oil filtration.
A separate kidney loop provides continuous filtration and optimum oil cleanliness at all times, supporting the hydraulic system.
ADVANCED HYDRAULIC SYSTEM
No excess oil flow
No excess high pressure oil
Lower hydraulic oil temperatures
Less cooling required
ADVANTAGES
Fuel Savings (20% MORE FUEL EFFICIENT)
Performance
Energy efficiency
Component life
Hydraulic Pump Utilization
Independent Oil Cooling System – Efficient Oil Cooling for Extended Component Life
Protect and Extend the Life of Your Hydraulic Components and Seals
Providing an efficient means of cooling, particularly in demanding applications, our unique independent oil cooling system will extend the life of your hydraulic shovel's components.
More Efficient Oil Cooling
Our system is independent of return oil, achieving efficiency through the utilization of dedicated pumps that provide cooling capacity as needed, whether the engine is idling or under load. That means optimum oil temperature is being maintained, even while your operator waits for the next truck to load. Competitive hydraulic shovels only provide cooling when the machine is working and the engine is under load.
Additional efficiency is achieved via:
Variable oil flow
Variable fan speed
Optimal Oil Temperature Maintained
Our unique independent oil cooling system ensures that system operating temperatures remain within the optimal operating viscosity range at all times.
Electronic Control System – Operate with Confidence
Enhanced Control Response and Optimized Hydraulic Engine Load Management
Help your team meet productivity and performance standards with our intuitive, informative on-board electronics.
Electro-hydraulic Servo Control
Enhanced Control Response Resulting in Increased Operator Comfort – The system relays actuating signals from the joysticks, delivering load independent and precise machine reactions that reduce operator fatigue.
Increased Up-time – Up-time is increased as a result of simplified troubleshooting and advanced diagnostic capabilities.
Clean and Quiet Cab Environment – No hydraulic lines are present in the cab or the cab module, ensuring a clean, odorless arrangement with less noise.
Control and Monitoring Platform (CAMP)
Reduced Control System Inventory – Streamlined system requires only two controllers for all functions (i.e., drive train and servo).
Less Fuel Consumption – Both engine and hydraulic pumps work in optimal range of performance during the entire digging cycle, reducing fuel burn.
Safety – Designed with Your Safety as Our Top Priority
Sharing your commitment to safety, and driven by our commitment to Zero Harm, we work tirelessly to design the safest machines possible to protect your most important asset; your employees.
Some examples of the safety-enhancing features of the Cat 6020B Hydraulic Mining Shovel include the following:
Operator Environment
Optimized operator situational awareness and safe machine positioning/truck-loading via class leading cab visibility.
Safe training environment facilitated by unobstructed view of digging environment and accessibility of emergency stop button from both seat belt equipped trainer seats.
Operator Protective Guard (Top Guard) certified cab with safety glass windshield.
Cab equipped with emergency hammer for quick escape and ready access to emergency ladder.
Machine Access
Safe access to shovel via retractable 45° stairway.
Safe access to power module components from machine platform and counterweight.
Safe movement about the machine via wide and slip-resistant walkways, limited walkway elevation changes (steps up/down), and minimized trip hazards.
Quick exit from machine during emergency facilitated by three means of egress.
Sound Suppression
Excellent power module and cab sound suppression system to protect operators and service personnel.
Electrical System
Safe electrical maintenance facilitated by lockable battery isolation and starter lockout switch.
Emergency Shut-offs
Multiple emergency stop buttons strategically located around machine for immediate engine shut-down, including a pull switch accessible from the ground.
Serviceability – Service Friendly for Greater Uptime
Designed to Start Producing Almost Immediately Upon Arrival on Site
The modular design of the 6020B facilitates quick field assembly. The average assembly time in typical conditions is 14 days; however, similar assembly times were achieved with pilot machines assembled at –30° C (–22° F).
Reduced Downtime Due to Exchangeable Power Module
Our exchangeable power module, which contains the most vital machine operating systems, can be quickly removed and replaced with a spare power module to increase machine uptime.
This capability also allows for transporting of the power module away from the production area to allow service and repair in a safe, convenient, and clean environment.
Service Friendly, with Unparalleled In-class Component Accessibility
The 6020B was designed to be easily serviced and maintained:
Exceptional component accessibility and weather protection via first-in-class and spacious walk-through power module.
Superior swing system component accessibility via boom-mounted hydraulic valve block.
Ground-level accessible service fluid fill points and jump start receptacle.
Automatic centralized lubrication system.
24 hour non-stop machine operation capability.
Extensive troubleshooting capability via hydraulic service ports.
Streamlined maintenance and parts availability with integrated Cat components.
Customer Support – Seamless Dealer Support
A Single Source for All Service and Maintenance Needs
With the use of Cat components throughout, you can rest assured that your local Cat dealer is your most knowledgeable and trusted single source for your 6020B service and maintenance needs. Cat dealer expert technicians have the unique knowledge, experience, training, and tooling necessary to fully support your 6020B hydraulic shovel, no matter the need or where your site is located.
Continued Support throughout the Life of Your 6020B
Consistent with any piece of Cat equipment, the 6020B is designed and built to provide maximum productivity, capability and operating economy throughout its working life. To help you meet these performance levels with your 6020B, Cat dealers offer a wide range of service plans that maximize uptime and return on your investment, including:
Preventative maintenance programs
Diagnostic programs, such as scheduled oil sampling and technical analysis
Rebuild and reman options
Customer support agreements
And although the 6020B is designed for easy operation, your Cat dealer can arrange training programs to help your operators improve productivity, increase uptime, reduce operating costs, and enhance safety.
No One Knows Your 6020B Hydraulic Shovel Better
The vast majority of Cat dealers across the globe have supported our line of hydraulic shovels for over a decade, so they are uniquely equipped to optimize the performance of your 6020B with their unmatched Cat hydraulic shovel expertise. This expertise includes a deep understanding of how the 6020B is best applied and utilized in all types of applications, so they can take your site-specific factors into account to help lower your operating and maintenance costs.
Parts Available When You Want Them
Receiving 6020B parts from your local Cat dealer is streamlined through the optimized use of Cat components, integrated part numbers, and stocking of parts in local Caterpillar warehouses. Your 6020B will be supported 24 hours a day, 7 days a week, by a worldwide network of parts distribution facilities, dealer service centers, and technical training facilities to keep it up and running at peak performance levels.
Drive System – Simple and Reliable System Supported Seamlessly
Simple and Cost-effective Single Engine Concept
When we asked you what design features you desired most from a 200 metric ton (220 short ton) size class hydraulic backhoe, a single-engine platform was a top request. We listened by designing the 6020B with a single C32 ACERT engine for reliable performance and simple and cost effective service when needed.
Reliable Cat C32 ACERT Engine
Delivering durable, reliable power that will keep your 6020B producing, the C32 ACERT has proven its ability to perform in harsh mining conditions throughout the world. Offering low operating costs, and supported 24/7 by your local Cat dealer, the C32 ACERT will help you achieve your production and profitability targets, reliably.
ACERT Technology
The development of ACERT Technology began with the search for a better way to reduce diesel engine emissions, and culminated in a revolutionary engine design breakthrough that burns fuel more precisely than ever before. Lower combustion temperatures reduce emissions and prolong the life of lighter, more power-dense engine platforms. It also varies the injection timing based on factors like engine load and speed for optimum performance under a wide range of operating conditions, including mining.
Worldwide Cat Engine Support
Our engines are only as good as the service and support that stand behind them. Highly trained and experienced service technicians at your local Cat dealership are ready with whatever you need, wherever and whenever you need it. They know the Cat C32 ACERT engine inside and out, so they can promptly diagnose issues and keep your 6020B running at peak performance.
Emissions Technology – Providing you reliable, integrated solutions.
The 6020B is offered with two variations of the C32 engine with ACERT Technology. One will meet Tier 4 Final emission standards and will be required for sale in higher regulated countries. The other option will emit equivalent to Tier 2 for lesser or non-regulated countries.
The 6020B meets Tier 4 Final emission standards using:
Cat NOx Reduction System – captures and cools a small quantity of exhaust gas, then routes it into the combustion chamber where it drives down temperatures and reduces NOx emissions.
Dual Diesel Oxidation Catalysts (DOCs) – use a chemical process called oxidation to condition exhaust gases to meet emission standards.
MEUI™-C Fuel System – delivers increased fuel efficiency, while further reducing NOx emissions. Ultra low sulfur diesel (ULSD) fuel and low ash oil are required.
The Tier 4 Final solution of the C32 ACERT engine has a maintenance free aftertreatment design, which uses the systems above to meet emissions standards. Designed to meet performance demands with lower cost of ownership, the primary advantages of this solution include:
Performance
Engines optimized for low fuel consumption at 1,800 rpm and lower speeds
Significant gains in fuel consumption delivered through collaboration of engine and machine integration
Maximum uptime, without work interruption for regeneration, engine derate, or cold weather treatment of secondary fluid
Lower service times and costs
Same long life to overhaul, with maintenance-free Diesel Oxidation Catalysts
No secondary fluid or storage tanks
No retrofit of current or purchase of new service truck to accommodate storage and delivery of secondary fluid
No expensive special treatment in cold climate areas due to freezing point of secondary fluid
Easy access filters
Cat MineStar System and Technology Solutions – Evolving Your Mine for Greater Safety and Productivity
Helping You Enhance Safety and Productivity through Technology
Aimed at enhancing the productivity and profitability of your 6020B hydraulic mining shovel, we currently offer a combination of Cat MineStar System offerings and Cat hydraulic mining shovel technology solutions.
Cat MineStar System
Helping you achieve your goals for enhanced mine site safety, improved efficiency, reduced operating costs, and greater profitability, the Cat MineStar System provides the most comprehensive suite of mining technology products in the industry. It consists of a number of configurable capability sets – Fleet, Terrain, Detect, Health, and Command – that allow you to scale the system to your mine site needs. Cat MineStar System helps you manage everything from material tracking to sophisticated real-time fleet management, machine health systems, autonomous equipment, and more.
The Cat 6020B is "MineStar ready", offering MineStar Health as a fully integrated option, as well as the Fleet, Terrain, and Detect as retrofit options.
Health – Health delivers critical event-based machine condition and operating data for your entire fleet. It includes comprehensive equipment health and asset monitoring capabilities with a wide range of diagnostic, analytic and reporting tools.
Fleet – Fleet provides real-time machine tracking, assignment and productivity management, providing a comprehensive overview of all your asset operations from anywhere in the world.
Terrain – Terrain enables high-precision management of drilling, dragline, grading and loading operations through the use of guidance technology. It increases machine productivity and provides you real-time feedback for improved efficiency.
Detect – Detect provides equipment operators with enhanced awareness for increased site safety, using a combination of radars, an in-cab display, and multiple cameras.
Please speak to your local dealer for more information on MineStar for the 6020B.
Hydraulic Shovel Technology Solutions
Monitoring and Diagnostic System – Enhancing diagnostic capabilities and providing detailed troubleshooting functions, our Board Control System uses sensors throughout the machine to monitor operating data, record faults, and notify the operator audibly and visually. This promotes the earliest possible detection of faults and allows for timely maintenance planning and assistance for speedy repair.
Swing System – Efficiency Enabling and Simplified Design
Enabling the Use of Advanced Hydraulics with an Open-loop Swing Circuit
The 6020B includes an open-loop swing circuit that interacts well with its newly designed advanced hydraulics. Utilizing patent-pending dedicated pump flow allocation technology, hydraulic pumps are allocated to individual circuits on demand, allowing all produced oil flow to be translated into cylinder motion, optimizing hydraulic efficiencies and reducing heat generation. To fully leverage the advantages of this innovative technology, the open-loop swing system was incorporated for its use of a common set of pumps to serve all functions and the flexibility it offers for utilization of hydraulic flow.
More Reliable Swing Component Life
Extending component life and ultimately improving machine uptime, our swing system includes a triple-race swing roller bearing with internal gearing connected to an automatic lubrication system.
For added reliability, all lube lines supplying the swing roller bearing are located inside the superstructure for maximum protection.
Undercarriage – Extended Component Life and Superior Serviceability
Tracks Designed for High-impact and High-travel Applications, Like Mining and Heavy Construction
Cat exclusive Positive Pin Retention 2 (PPR2) Track design resists pin walking and link cracking for reliable sealing and maximum track life.
– Resists end-play generation and link movement on the pin
– Tightly controls seal motion for long internal pin/bushing wear life
– Resists fatigue and crack formation with redesigned, stronger track links
Better Wear of Undercarriage Components
Even idler slide wear and extended component life result from the floating push tube.
Low wear drive system via induction hardened and high quantity of sprocket teeth.
Optional rough terrain undercarriage protection kit available to further protect undercarriage components from harsh ground conditions.
Superior Serviceability
The 6020B's automatic track tensioning system is a simplified design that requires no manual adjustment.
Service simplified by externally serviceable break.
PPR2 Tracks are easily serviced with a master joint. Allows for easy removal and installation of undercarriage.
Reliable Crawler Performance
Eliminates unnecessary wear and assists in easier track tensioning via three carrier rollers.
Exceptional track guidance via standard track guides the entire length of the crawler.
Travel motors and gearboxes are well protected by robust steel covers.
Cat Buckets and Ground Engaging Tools – Improved Productivity, Operational Efficiency, and Serviceability
Cat Buckets Increase Productivity
Cat buckets are designed to match your Cat 6020B mining shovel, providing optimum payload and machine efficiency while protecting your investment. Bucket wear surfaces are armored with replaceable wear materials to extend the life of your bucket. Cat buckets are easy to rebuild, with all parts available through your Cat dealer. Trust Cat to give you long service life without adding excessive weight.
Key Features:
Sized to match the 6020B mining shovel and your application
Cat G.E.T. systems
Various wear packages available to meet your site-specific requirements
G.E.T. Quality and Performance Made Easy
Increase your operational efficiency and productivity with hammerless Cat G.E.T. designed specifically for the 6020B hydraulic mining shovel. By designing our own G.E.T., we are able to take a production focus, rather than a component focus, to optimize performance across the entire machine. And like all Cat G.E.T., it is fully supported by your local Cat dealer.
Simple: No special tools required for Removal & Install
Fast: One turn to lock and unlock
Safe: No hammer required to service the lip system
Options: Four tip shapes to optimize your production
Machine Structures – Durability You Can Rely On
Large and Robust Structures Designed and Fabricated to Withstand Your Toughest Digging Conditions
To extend service life and ensure that your 6020B keeps producing, our structures are designed for durability and dependability. Extended performance in the harsh digging conditions you face daily is accomplished through selection of high-strength steels and rugged castings, joined and thermally stress-relieved to create a reliable external shell.
Manufactured from high-strength steel for durability.
Full penetration, profiled and ground welds at critical junctures.
MT, UT, and X-ray inspections on select welds ensure quality.
Reliable Front Attachment Structures
The 6020B boom and stick utilize high-strength steel and rugged castings that are joined and thermally stress relieved for optimum structural life.
Heavy castings at all pivot points.
Single-plate side walls.
Better flow of forces and less welding seams, as top chords are made of one bend plate.
Entire boom and stick are stress relieved after welding for maximized reliability.
Extensive use of Finite Element Analysis (FEA).
Fully Tested and Validated
All 6020B structures have been fully tested and validated at our state-of-the-art proving ground in Tucson, AZ (U.S.A.).
Loading/Hauling Efficiency – Move More Material with Optimal Pass Match Pairings
Achieve Targeted Loading/Hauling Production with Perfectly Paired Cat Hydraulic Shovels and Mining Trucks
For full truck payloads with minimum loading time, an efficient loading/hauling system begins with an optimized equipment match. Cat hydraulic shovels are matched with Cat mining trucks to maximize volume of material moved at the lowest operating cost per ton.
The 6020B was designed to be an optimal pass-match with our popular 777 Series off-highway truck. It is also capable of pairing with the 785 Series mining truck, where applicable.
Expanded Offerings with Specialty Solutions – Power and Precision to Create Solutions beyond the Core.
Flexible offerings accommodate various specialty front arrangements and the capability to work in mobile or fixed applications. With industry leading tool carrying capacity and reliability, HMS Specialty Solutions are ideally positioned to move more material at a lower cost and maximize profitability.
Versatile in nature, shovel solutions:
are designed with safety as top priority
have a proven durability you can rely on
are supported by an unparalleled network of dealers
are protected by Caterpillar’s standard warranty
Frontless Shovel Arrangements
Frontless shovel arrangements integrated with non-standard front attachments, work tools, and technology can create optimized solutions for various high power applications.
In addition to the base carrier, solutions generally include Caterpillar cylinders, components and worktools.
Common applications best served with these solutions include long reach, rock placement or removal, bulk material handling, and demolition.
Upper Only Arrangements for Fixed Installations
Upper only arrangements integrated with non-standard front attachments can be fixed or pedestal mounted to create mechanical dredging and bulk material handling solutions.
The standard carbody can be integrated as a structural mounting platform and be supplied with or without the swing system.
Undercarriage and Track Arrangements
Mobile undercarriage options provide efficient hydraulic power in track arrangements or complete mobile platforms to support loads over 170 tonnes (187 tons). Solutions include: complete undercarriage or individual components (carbody, track sides, or ring gear).
Inhouse performance analysis ensures solution is sized appropriately for application and payload.
Durable and designed for long life, components are easier to assemble and field install.
Common solutions best served with undercarriage or track arrangements include, but are not limited to, conveyors and crushers.
Identify the task and tool. We have the rest. Problem Solved.
Sustainability – Higher Standards for a Better Tomorrow
Meeting the needs of today without compromising the needs of tomorrow is the goal for all Cat machinery. The commitment to helping you operate safely and sustainably is affirmed in the design of the 6020B hydraulic mining shovel.
Cat 6020B Sustainability
Rebuilds – Decrease your energy use and material consumption with a machine design that facilitates rebuilding.
Service – Ground-level accessible service fluid fill points ensure fast, easy, and secure replenishment of machine fluids.
Sound Levels – Reduced operator and spectator sound levels result in less impact on the communities where they operate. The 6020B provides sound suppression on its power module to keep spectator sound levels low, and provides a sound suppressed cab for an extremely quiet working environment for the operator.
Component Life – The 6020B's automatic centralized lubrication system maintains the proper grease lubrication on working surfaces, significantly extending component life.
Product Parameter
Overview
You need a shovel that works. A simple, durable digger that gets the job done efficiently and safely. The Cat 6020B is engineered from the ground up with ease of use in mind. It's easy to assemble, easy to learn, easy to operate and easy to maintain. So you can concentrate on running a safe, productive operation. The new Cat 6020B. It's not complicated.
General
Units:
Engine Output - SAE J1995 | 778 kW (1,043 hp) 778 kW (1,043 hp) | More |
Standard Bucket Capacity | Backhoe (heaped 1:1) 12.0 m³ (15.7 yd³) Backhoe (heaped 1:1) 12.0 m³ (15.7 yd³) | More |
Operating Weight | Backhoe –230 tonnes (254 tons) Backhoe –230 tonnes (254 tons) | More |
Electrical System
Batteries (12V each) | 6 × 210 Ah 6 × 210 Ah | More |
Batteries (12V each) - In Series/Parallel Installation | 630 Ah – 24V 630 Ah – 24V | More |
Battery Isolation Relays | manual lockable disconnect switch and automatic disconnect relay manual lockable disconnect switch and automatic disconnect relay | More |
Components (1) | Emergency stop buttons inside cab, accessible from all seating locations, and engine module Emergency stop buttons inside cab, accessible from all seating locations, and engine module | More |
Components (2) | Additional ground-level emergency stop Additional ground-level emergency stop | More |
Components (3) | 9 LED high-brightness working flood lights: – 7 for working area – 2 for rear end 9 LED high-brightness working flood lights: – 7 for working area – 2 for rear end | More |
System Voltage | 24V 24V | More |
Components (4) | 2 LED high-brightness access flood lights 2 LED high-brightness access flood lights | More |
Components (5) | 7 LED service lights 7 LED service lights | More |
Components (6) | 1 beacon lamp on cab roof 1 beacon lamp on cab roof | More |
Hydraulic Oil Cooling
Diameter - Fan | 4.92 ft 1500.0 mm | More |
Features (1) | Cooling system fully independent of all main circuits, i.e. controlled cooling capacity available whenever engine is running Cooling system fully independent of all main circuits, i.e. controlled cooling capacity available whenever engine is running | More |
Features (2) | Variable electronically controlled flow of oil through cooler and fan speed Variable electronically controlled flow of oil through cooler and fan speed | More |
Features (3) | Superior cooling efficiency to ensure optimum oil temperature Superior cooling efficiency to ensure optimum oil temperature | More |
Oil Flow of Cooling Pumps | 211.0 gal/min 800.0 l/min | More |
Operator's Cab
Components (1) | Large cab floor window with removable grating for easy cleaning Large cab floor window with removable grating for easy cleaning | More |
Components (10) | Machine access via retractable access stairway, stairway angle approximately 45°, hydraulically operated Machine access via retractable access stairway, stairway angle approximately 45°, hydraulically operated | More |
Components (11) | Additional emergency ladder in close proximity to emergency escape window Additional emergency ladder in close proximity to emergency escape window | More |
Components (2) | Pneumatically cushioned and multi-adjustable operator seat with lumbar support, safety belt, head- and armrests Pneumatically cushioned and multi-adjustable operator seat with lumbar support, safety belt, head- and armrests | More |
Components (3) | Safety switch in operator's seat for automatic motion shutdown Safety switch in operator's seat for automatic motion shutdown | More |
Components (4) | Joystick integrated in adjustable seat armrest Joystick integrated in adjustable seat armrest | More |
Components (5) | Full sized trainer seat with safety belt and work table Full sized trainer seat with safety belt and work table | More |
Components (6) | Auxiliary fold-away seat with safety belt for 3rd person Auxiliary fold-away seat with safety belt for 3rd person | More |
Components (7) | Operator Protective Guard (rock guard; approved according to ISO 10262:1998 [Top Guard]) compliant Operator Protective Guard (rock guard; approved according to ISO 10262:1998 [Top Guard]) compliant | More |
Components (8) | Windshield with parallel intermittent wiper/washer Windshield with parallel intermittent wiper/washer | More |
Components (9) | Roller blinds Roller blinds | More |
Internal Dimensions of Cab - Height | 6.79 ft 2070.0 mm | More |
Internal Dimensions of Cab - Length | 7.32 ft 2230.0 mm | More |
Internal Dimensions of Cab - Width | 5.33 ft 1625.0 mm | More |
New BCS Features (1) | Robust instrument panel including large (254 mm/10 in) color touch screen Robust instrument panel including large (254 mm/10 in) color touch screen | More |
New BCS Features (2) | On-screen troubleshooting assistance On-screen troubleshooting assistance | More |
New BCS Features (3) | Graphical data logging Graphical data logging | More |
New BCS Features (4) | Fault memory capabilities Fault memory capabilities | More |
New BCS Features (5) | USB, Lan (TCP/IP) and CAN BUS interfaces for data export USB, Lan (TCP/IP) and CAN BUS interfaces for data export | More |
New Board Control System (BCS) Features: | Electronic monitoring, data logging and diagnostic system for vital signs & service data of engines, hydraulic & lube system Electronic monitoring, data logging and diagnostic system for vital signs & service data of engines, hydraulic & lube system | More |
Operator's Eye Level (approximate) | 18.04 ft 5.5 m | More |
Swing System
Features (1) | Open swing circuit with auto slow down when joysticks in neutral Open swing circuit with auto slow down when joysticks in neutral | More |
Features (2) | All slew ring raceways and grease tub for internal gearing supplied by automatic, central lubrication system All slew ring raceways and grease tub for internal gearing supplied by automatic, central lubrication system | More |
Maximum Swing Speed | 4.9 r/min 4.9 r/min | More |
Parking Brake | Wet multiple-disc brake, spring-loaded/hydraulically released Wet multiple-disc brake, spring-loaded/hydraulically released | More |
Swing Drive | 2 compact planetary transmissions with axial piston motors 2 compact planetary transmissions with axial piston motors | More |
Swing Ring | Triple-race roller bearing with sealed internal gearing Triple-race roller bearing with sealed internal gearing | More |
Undercarriage
Bottom Rollers - Each Side | 8 8 | More |
Components (1) | Forged double-grouser track pads Forged double-grouser track pads | More |
Components (2) | Chain links connected by hardened pins and bushings Chain links connected by hardened pins and bushings | More |
Components (3) | All running surfaces of sprockets, idlers, rollers and track chain links hardened All running surfaces of sprockets, idlers, rollers and track chain links hardened | More |
Components (4) | Fully hydraulic self-adjusting track tensioning system with accumulator Fully hydraulic self-adjusting track tensioning system with accumulator | More |
Components (5) | Automatic hydraulic retarder valve to prevent overspeed on downhill travel Automatic hydraulic retarder valve to prevent overspeed on downhill travel | More |
Components (6) | Audible travel alarm Audible travel alarm | More |
Gradeability - Travel Drives | Approximately 54% Approximately 54% | More |
Maximum Tractive Force | 265860.0 1183.0 kN | More |
Parking Brakes | Wet multiple disc brake, spring loaded/hydraulically released Wet multiple disc brake, spring loaded/hydraulically released | More |
Support Rollers - Each Side | 3 3 | More |
Track Pads - Each Side | 45 45 | More |
Travel Drives - Each Side | 1 planetary transmission with 2 two-stage axial piston motors 1 planetary transmission with 2 two-stage axial piston motors | More |
Travel Speed - 1st Stage - Maximum | 0.68 mile/h 1.1 km/h | More |
Travel Speed - 2nd Stage - Maximum | 1.49 mile/h 2.4 km/h | More |
Automatic Lubrication System
Capacity - Grease Barrel | 54.0 gal (US) 205.0 l | More |
Type (1) | Single-circuit progressive system with hydraulically driven heavy-duty pump and electronic time control Single-circuit progressive system with hydraulically driven heavy-duty pump and electronic time control | More |
Type (2) | Grease supplied to swing roller bearing, all pivot points of attachment, and swing gearbox bearing Grease supplied to swing roller bearing, all pivot points of attachment, and swing gearbox bearing | More |
Type (3) | System condition and failures displayed by Board Control System System condition and failures displayed by Board Control System | More |
Attachment
Buckets Equipped With | – Special liner material covering main wear areas inside and outside – Lip shrouds – Wing shrouds – Heel shrouds – Special liner material covering main wear areas inside and outside – Lip shrouds – Wing shrouds – Heel shrouds | More |
Type (1) | Boom and stick torsion-resistant with welded box design Boom and stick torsion-resistant with welded box design | More |
Type (2) | High-tensile steel with solid steel castings at pivot areas High-tensile steel with solid steel castings at pivot areas | More |
Type (3) | Boom and stick stress-relieved after welding Boom and stick stress-relieved after welding | More |
Type (4) | Catwalks with rails at boom Catwalks with rails at boom | More |
Type (5) | Float valve for boom down function Float valve for boom down function | More |
Operating Weights - Backhoe
Ground Pressure | 31.9 psi 22.0 N/cm² | More |
Operating Weight | 507500.0 lb 230200.0 kg | More |
Standard Track Pads | 2.62 ft 800.0 mm | More |
Hydraulic System with Electronic Pump Management
Electronic Pump Management Contains (1) | Electronic load limit control Electronic load limit control | More |
Electronic Pump Management Contains (2) | Dedicated circuit pump allocation Dedicated circuit pump allocation | More |
Electronic Pump Management Contains (3) | Automatic return of main pumps to zero flow Automatic return of main pumps to zero flow | More |
Electronic Pump Management Contains (4) | Automatic rpm reduction of engine speed during working breaks Automatic rpm reduction of engine speed during working breaks | More |
Electronic Pump Management Contains (5) | Reduced oil flow of main pumps at high hydraulic oil temperature and at high engine temperature Reduced oil flow of main pumps at high hydraulic oil temperature and at high engine temperature | More |
Features (1) | Pressure cut-off function for all main pumps Pressure cut-off function for all main pumps | More |
Features (2) | Cooling of pump transmission gear oil Cooling of pump transmission gear oil | More |
Filters (1) | Full-flow high-pressure filters (100 μm) for main pumps, installed directly behind each pump Full-flow high-pressure filters (100 μm) for main pumps, installed directly behind each pump | More |
Filters (2) | Full-flow filters (10 μm) for complete return circuit Full-flow filters (10 μm) for complete return circuit | More |
Filters (3) | Full-flow filters (10 μm) for cooling return circuit Full-flow filters (10 μm) for cooling return circuit | More |
Filters (4) | Pressure filters (6 μm) for servo circuit Pressure filters (6 μm) for servo circuit | More |
Filters (5) | Transmission oil filter (40 μm) Transmission oil filter (40 μm) | More |
Main Pumps | 6 × variable swash plate pumps 6 × variable swash plate pumps | More |
Maximum Pressure - Attachment | 4495.0 psi 310.0 bar | More |
Maximum Pressure - Swing - Acceleration | 4495.0 psi 310.0 bar | More |
Maximum Pressure - Travel | 4495.0 psi 310.0 bar | More |
Maximum Swing Oil Flow | 216.0 gal/min 783.0 l/min | More |
Maximum Total Oil Flow | 621.0 gal/min 2350.0 l/min | More |
Hydraulic Tank Capacity | 740.0 gal (US) 2800.0 l | More |
Maximum Pressure - Swing - Deceleration | 5080.0 psi 350.0 bar | More |
Total Volume of Hydraulic Oil | 925.0 gal (US) 3500.0 l | More |
Centralized Service Area
Equipped With (1) | Quick couplings for: – Diesel fuel – Engine coolant – Pump transmission gear oil – Engine oil (oil pan) – Hydraulic oil Quick couplings for: – Diesel fuel – Engine coolant – Pump transmission gear oil – Engine oil (oil pan) – Hydraulic oil | More |
Equipped With (2) | Cat jump-start socket Cat jump-start socket | More |
Equipped With (3) | Indicator light for hydraulic tank full Indicator light for hydraulic tank full | More |
Features | Centralized service area accessible from ground level. Centralized service area accessible from ground level. | More |
Diesel Engine - Equivalent to Tier 2
Alternator | 275A 275A | More |
Aspiration | Turbocharged and air-to-air aftercooled Turbocharged and air-to-air aftercooled | More |
Bore | 5.71 in 145.0 mm | More |
Components (1) | Hydraulically driven radiator fan with variable electronically controlled fan speed Hydraulically driven radiator fan with variable electronically controlled fan speed | More |
Components (2) | Micro processed engine management Micro processed engine management | More |
Components (3) | Heavy-duty air filters Heavy-duty air filters | More |
Components (4) | Two-stage fuel filter Two-stage fuel filter | More |
Components (5) | Additional high-capacity water separator including electric priming pump Additional high-capacity water separator including electric priming pump | More |
Components (6) | Large fuel tank allows for 24 hour machine operation Large fuel tank allows for 24 hour machine operation | More |
Displacement | 1959.0 in³ 32.0 l | More |
Emissions | Meets China Nonroad Stage III emissions standards, equivalent to Tier 2 Meets China Nonroad Stage III emissions standards, equivalent to Tier 2 | More |
Fuel Tank Capacity | 951.0 gal (US) 3600.0 l | More |
Gross Power - SAE J1995 | 1040.0 HP 776.0 kW | More |
Make and Model | Cat C32 ACERT Cat C32 ACERT | More |
Maximum Altitude without Deration | 3622 m (11,884 ft) – above sea level (a.s.l.) 3622 m (11,884 ft) – above sea level (a.s.l.) | More |
Net Power - ISO 9249 | 1037.0 HP 774.0 kW | More |
Net Power - SAE J1349 | 1032.0 HP 770.0 kW | More |
No. of Cylinders | 12 12 | More |
Rated Speed | 1800 min-1 (1,800 rpm) 1800 min-1 (1,800 rpm) | More |
Stroke | 6.38 in 162.0 mm | More |
Diesel Engine - Tier 4 Final
Alternator | 275A 275A | More |
Aspiration | Turbocharged and air-to-air aftercooled Turbocharged and air-to-air aftercooled | More |
Bore | 5.71 in 145.0 mm | More |
Components (1) | Cat NOx reduction system Cat NOx reduction system | More |
Components (2) | Dual Diesel Oxidation Catalysts (DOCs) Dual Diesel Oxidation Catalysts (DOCs) | More |
Components (3) | MEUI™-C fuel system MEUI™-C fuel system | More |
Components (4) | Hydraulically driven radiator fan with variable electronically controlled fan speed Hydraulically driven radiator fan with variable electronically controlled fan speed | More |
Components (5) | Micro processed engine management Micro processed engine management | More |
Components (6) | Heavy-duty air filters Heavy-duty air filters | More |
Components (7) | Two-stage fuel filter Two-stage fuel filter | More |
Components (8) | Additional high-capacity water separator including electric priming pump Additional high-capacity water separator including electric priming pump | More |
Components (9) | Large fuel tank allows for 24 hour machine operation Large fuel tank allows for 24 hour machine operation | More |
Displacement | 1959.0 in³ 32.0 l | More |
Emissions | Meets Tier 4 Final and Stage V emissions standards Meets Tier 4 Final and Stage V emissions standards | More |
Fuel Tank Capacity | 951.0 gal (US) 3600.0 l | More |
Gross Power - SAE J1995 | 1033.0 HP 771.0 kW | More |
Make and Model | Cat C32 ACERT Cat C32 ACERT | More |
Maximum Altitude without Deration | 2925 m (9,600 ft) – above sea level (a.s.l.) 2925 m (9,600 ft) – above sea level (a.s.l.) | More |
Net Power - ISO 9249 | 1024.0 HP 764.0 kW | More |
Net Power - SAE J1349 | 1019.0 HP 761.0 kW | More |
No. of Cylinders | 12 12 | More |
Rated Speed | 1,800 min-1 (1,800 rpm) 1,800 min-1 (1,800 rpm) | More |
Stroke | 6.38 in 162.0 mm | More |
Engine - Equivalent to U.S. EPA Tier 2
Engine Model | Cat C32 ACERT Cat C32 ACERT | More |
Gross Power - SAE J1995 | 1040.0 HP 776.0 kW | More |
Net Power - SAE J1349 | 1032.0 HP 770.0 kW | More |
Engine - U.S. EPA Tier 4 Final
Engine Model | Cat® C32 ACERT™ Cat® C32 ACERT™ | More |
Gross Power - SAE J1995 | 1033.0 HP 771.0 kW | More |
Net Power - SAE J1349 | 1019.0 HP 761.0 kW | More |
Bucket
Standard Bucket Capacity - Backhoe (Heaped 1:1) | 15.7 yd³ 12.0 m³ | More |
Digging Forces
Maximum Breakout Force | 164050.0 lb 730.0 kN | More |
Maximum Tearout Force | 146125.0 lb 650.0 kN | More |
Operating Specifications
Bucket Payload | 24.0 Sh Ton 22.0 t | More |
Operating Weight | 254.0 ton (US) 230.0 t | More |
Working Ranges
Maximum Digging Depth | 26.57 ft 8.1 m | More |
Maximum Digging Height | 45.6 ft 13.9 m | More |
Maximum Digging Reach | 52.17 ft |